001 ข้อดีของงานที่อบชุบด้วยเตาสูญญากาศ
- ผิวสะอาด
- งานไม่สูญเสียคาร์บอนออกไป
- ไม่เกิดอ๊อกซิเดชั่น
- เกิดการเปลี่ยนรูปน้อย
- แก้ไขและเปลี่ยนแปลงง่าย
- สามารถบัดกรีแข็งภายใต้สูญญากาศที่อุณหภูมิสูงได้
- ประหยัด
|
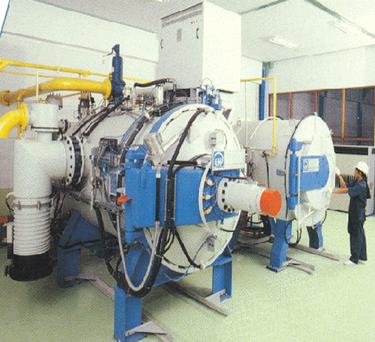 |
002 ข้อมูลทางด้านเทคนิคของเตา VKNQ |
- พื้นที่บรรจุงาน 650x600x900 มม.
- น้ำหนักบรรจุสูงสุด 650 กก.
- อุณหภูมิใช้งานสูงสุด 1,300 oC
- ความเที่ยงตรงของอุณหภูมิ <+5 oK
- ชุบด้วยแก๊สไนโตรเจนความดัน 6~10 บาร์
- สามารถทำสูญญากาศได้ถึง 10-2~10-5 mbars
จัดสร้างโดย ALD (เยอรมัน)
|
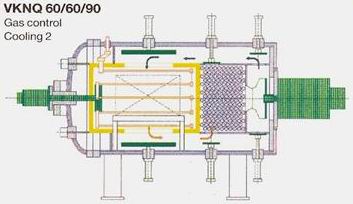 |
003 กระบวนการ ให้ความร้อนด้วยการพา |
- การส่งผ่านความร้อนด้วยการแผ่รังสีเพียงอย่าง
เดียวภายใต้สูญญากาศ จะไม่ได้ผลที่อุณหภูมิต่ำ กว่า 500 oC และยังผลให้อุณหภูมิที่ผิว และแกน ของชิ้นงานมีความแตกต่างกันมาก ผลของความแตกต่างของอุณหภูมิดังกล่าวทำ ให้เกิดความเค้น (Thermal Stress) ซึ่งอาจจะเป็น ต้นเหตุทำให้เกิดการบิดงอของชิ้นงาน
- โดยการเพิ่มแก๊สไนโตรเจนความดัน 2 บาร์เข้าไป
เพื่อทำให้เกิดการส่งผ่านความร้อนด้วยการพา ซึ่ง ทำให้การให้ความร้อนเป็นไปอย่างรวดเร็ว สม่ำเสมอ และทั่วถึง
|
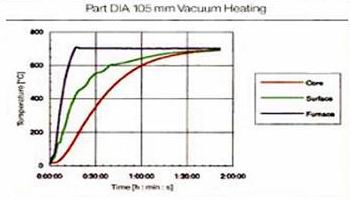
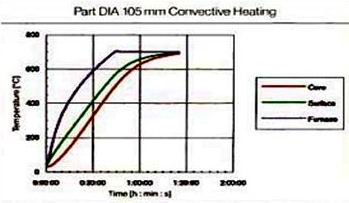 |
004 กระบวนการชุบแบบ มาร์เคว้นชิ่ง |
- ในกรณีที่ชิ้นงานมีขนาดใหญ่ และรูปร่างสลับซับ
ซ้อน การชุบให้เย็นตัวอย่างรวดเร็วทันที่ทันใด อาจจะ เป็นสาเหตุของการแตกร้าวและ/หรือการบิดงอของ ชิ้นงานอย่างรุนแรง
- การชุบโดยให้เย็นตัวลงมาที่ระดับเหนือจุดมาร์เทน
ไซด์เริ่มต้นของวัสดุ ซึ่งควบคุมด้วยโปรแกรมโดยการ ติดตั้งเทอร์โมคับเปิล์สองเส้นไว้ที่ผิวและแกนของชิ้น เทียบเคียง(Dummy) ซึ่งบรรจุเข้าไปพร้อมกับชิ้นงาน เป็นการชุบที่ทำให้การเกิดการบิดงอของชิ้นงานน้อยที่สุด
|
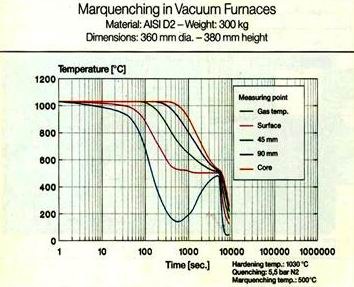 |
005 กระบวนการ สลับทางของการชุบ |
- ในขั้นตอนของการชุบนั้นเหล็กกล้าจะต้องถูกชุบให้เย็นตัว ในอัตราที่รวดเร็วและช้าเท่าที่จะสามารถกระทำได้
- ใช้อัตราการเย็นตัวที่เร็วเพียงพอเพื่อให้ได้โครงสร้างที่ สมบูรณ์และช้า ๆ หลังจากนั้น เพื่อป้องกันการแตกร้าว และการบิดงอต่าง ๆ ของชิ้นงาน
- เตาของเราสามารถควบคุมได้ทั้งสองอย่างคือทำการชุบ ด้วยแก๊สความดันสูงพร้อมกับการสลับทิศทาง ของการชุบ ด้วยโปรแกรมที่กำหนดตลอดจนการชุบแบบมาร์เคว้นชิ่ง
|
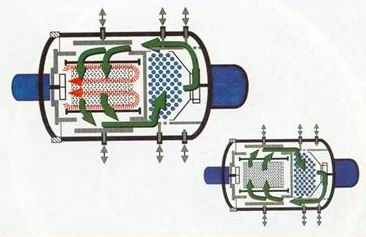 |
006 องค์ประกอบ การอบชุบด้วยความร้อนของ เหล็กกล้าเครื่องมือส่วนผสมสูง |

- การชุบแข็งเหล็ก เครื่องมือ ส่วนผสมสูง จำเป็นที่จะต้องกระทำภายใต้กระบวนการสูญญากาศ เพื่อที่จะหลีกเลี่ยงการเกิดอ๊อกซิ
เดชั่น และการสูญเสียธาตุคาร์บอน
- ในกระบวนการภายใต้สูญญากาศของเราใช้ชิ้นเทียบเคียงซึ่งมี เทียบเคียงซึ่งมีขนาดที่มีความโตเท่ากับชิ้นงานที่จะทำการชุบ
แข็งโดย ติดตั้งเทอร์โมคับเปิล์สองเส้นไว้ที่ผิวและแกน ซึ่งเทอร์โมคับเปิล์ดังกล่าวสามารถที่จะจัดการควบคุมอุณหภูมิ ที่ผิวและแกนของชิ้นงาน จนตลอดทั้งกระบวนการของการชุบแข็ง โดยวิธีการนี้เราสามารถที่จะ ; -
1. จัดการเกี่ยวกับความเค้นอันเนื่องจากความร้อนซึ่งเกิดขึ้น ในขณะที่ให้ความร้อนแก่ชิ้นงาน และทำให้เกิดการบิดงอน้อยลง 2. ป้องกันการเกิดโครงสร้างออสเทนไนท์ ไม่เพียงพอที่แกนและการเกิดการละลายของคาร์ไบด์ในโครงสร้างออสเทนไนท์ที่ มากเกินไป โดยการควบคุมอุณหภูมิของการเกิดโครงสร้างออสเทนไนท์ที่แกน 3. ประยุกต์ใช้กระบวนการมาร์เคว้นชิ่งเพื่อที่ จะป้องกันการแตกร้าวและลดการบิดงอ อันเกิดจากทั้งความเค้นที่เกิดจากความร้อน และการเปลี่ยนแปลงโครงสร้าง ในกรณีของชิ้นงานที่มีรูปร่างสลับซับซ้อน
การอบคืนไฟที่อุณหภูมิสูงจำนวน 3 ครั้งเป็นกฎทั่วไปของการทำงาน การอบคืนไฟครั้งที่ 1 เพื่อที่จะแยกสลายออสเทนไนท์ที่ ตกค้าง ซึ่งไม่สามารถที่จะหลีกเลี่ยงได้ในเหล็กคาร์บอนสูง และเหล็กกล้าเครื่องมือส่วนผสมสูง โดยการอบคืนไฟครั้งที่ 2 เรา ทำเพื่อควบคุมให้ ได้ความแข็งตามต้องการ การอบคืนไฟครั้งที่ 3 คือการอบคลายความเค้น เพื่อที่จะป้องกันการเกิดการแตกร้าว และการเปลี่ยนรูปตลอดกระบวนการที่ต่อเนื่องในภายหลัง |
007 เหล็กกล้าเครื่องมืองานร้อน |

- ส่วนมากเหล็กกล้าเครื่องมืองานร้อนมีความสามารถ ในการชุบแข็งสูง และสามารถที่จะทำการชุบแข็งด้วยแก๊ส ในกระบวนการภายใต้สูญญากาศ ประกอบกับขนาดของแม่พิมพ์ที่ใหญ่ขึ้น และปัญหาการแตกร้าวระยะแรก (EARLY CRACKING) ได้เกิดขึ้น ดังนั้นความเร็วในการชุบเป็นสิ่งที่จำเป็นจะต้องนำมา
พิจารณา
- สืบเนื่องจากแผนภูมิ CCT ด้านขวามือ การเกิดโครงสร้าง
เบไนท์ เกิดขึ้นในขั้นตอนที่เร็วกว่า การเกิดโครงสร้าง เพิลไลท์ และมันจะประกอบด้วย โครงสร้างออสเทนไนท์ที่ตกค้างอยู่ในเนื้อพื้น (MATRIX)จำนวนหนึ่ง การเกิดการรวมตัวของคาร์ไบด์ที่บริเวณขอบ เกรนของออสเทนไนท์ อันเนื่องมาจากการอบคืนไฟ เป็นสาเหตุของการเกิดการแตกร้าวระยะแรก (EARLY CRACKING)
|
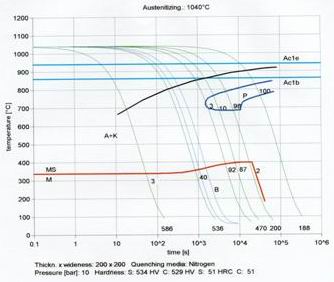 |
008 เหล็กกล้าเครื่องมืองานเย็น |

- ในการชุบแข็งเหล็กชนิดนี้ไม่สามารถ ที่จะหลีกเลี่ยง
โครงสร้าง ออสเทนไนท์ที่ตกค้างได้ เพราะว่ามีส่วนผสม และคาร์บอนสูง
- บ่อยครั้งโครงสร้างออสเทนไนท์ที่ตกค้าง เป็นต้นเหตุของการแตกร้าว และการเปลี่ยนรูปของชิ้นงาน โดยเฉพาะชิ้นงานที่จะต้องไปทำ Wire Cut หรือเจียรไน การทำ Subzero Treatment หรือการอบคืนไฟที่อุณหภูมิสูงจำนวน 2 ครั้ง สำหรับชิ้นงานดังกล่าวมีความจำเป็นอย่างยิ่ง
- โดยการอบคืนไฟที่อุณหภูมิสูง ความแข็งที่ได้ จะอยู่ในช่วง 55~58 HRC ถ้าหากต้องการความแข็งถึง 60 HRC
อุณหภูมิ ในการชุบแข็งจะต้องใช้ถึง 1,070 oC ซึ่งจะสูงกว่าอุณหภูมิ ชุบแข็งปกติคือ 1,030 oC ทั้งนี้ เพื่อที่จะให้ได้ความแข็ง อันเนื่องมาจากการเกิด second hardening กระบวนการเช่นนี้ไม่แนะนำ เพราะเป็นการเพิ่มปริมาณของโครงสร้างออสเทนไนท์ ที่ตกค้าง
- การอบคลายความเค้นจะกระทำสำหรับ กระบวนการแปรรูป ด้วยเครื่องมือกลที่ต่อจากการชุบแข็ง
|
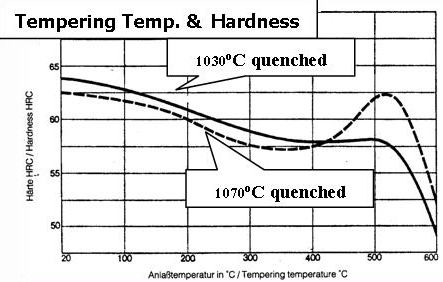 |
009 เหล็กไฮสปีด |

- เหล็กไฮสปีดได้ถูกพัฒนาขึ้นมาสำหรับเครื่องมือตัด ซึ่งสามารถที่จะรักษาความแข็งที่สูงเอาไว้ ถึงแม้ว่าได้รับความร้อนถึงสภาพ ร้อนแดงโดยอันเนื่องมาจากการตัดที่ ใช้ความเร็วรอบสูง เพื่อวัตถุประสงค์นี้ อุณหภูมิชุบแข็ง จำเป็นจะต้องกระทำที่อุณหภูมิ 1,200 oC เพื่อต้องการความแข็งสูง
- การอบคืนไฟ จะต้องกระทำมากกว่า 3 ครั้ง เป็นเพราะเหล็กกล้าชนิด นี้มีปริมาณของโครงสร้างออสเทนไนท์ที่ตกค้าง ภายหลังชุบแข็งเป็นจำนวนมาก
- เครื่องมือตัดบาง ๆ สามารถที่จะทำการ ดัดได้โดยอาศัยคุณสมบัติของ โครงสร้างออสเทนไนท์ที่ตกค้างหลังจาก การชุบในขณะที่ยังอุ่นอยู่
- เหล็กไฮสปีดเมื่อใช้งาน ที่ไม่เกิดความร้อน (ROOM TEMPERATURE) และต้องการความแกร่ง จะต้องใช้อุณหภูมิ ชุบแข็งที่ต่ำกว่าปกติ ซึ่งกระบวนการสำหรับความ แกร่งสูงนี้เรียกว่า UNDER HARDENING
|
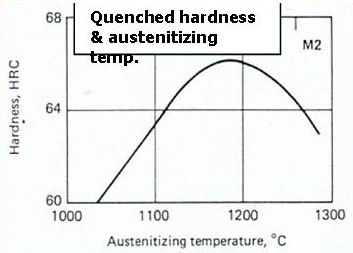
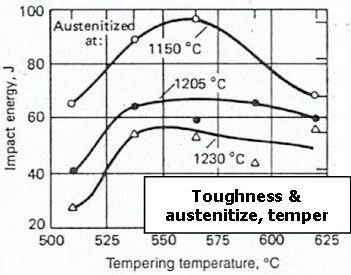 |
010 |

- ฟิล์มของอ๊อกไซด์บนผิวของโลหะชิ้นงาน จะถูกขจัดโดยสูญญากาศ และผิวผนังของมันถูกอาบ ไปด้วยตัวประสาน (ALLOY) เป็นผลทำให้เกิด การเชื่อมประสานที่ดี
- ด้วยการให้ความร้อนแก่ ชิ้นงานที่อุณหภูมิสูงภายใต้ สูญญากาศที่เพียงพอแก่การแพร่ กระจายของโลหะทำให้เกิดการเชื่อม
ประสานที่ปราศจากสารมลทิน และเกิดโพรงภายใน
- ช่องว่าง (GAP) แคบ ๆ ที่มีค่าน้อยกว่า 0.05 มม. ทำให้การเชื่อมประสานของโลหะมีความแข็งแรง และความเที่ยงตรงสูง
|
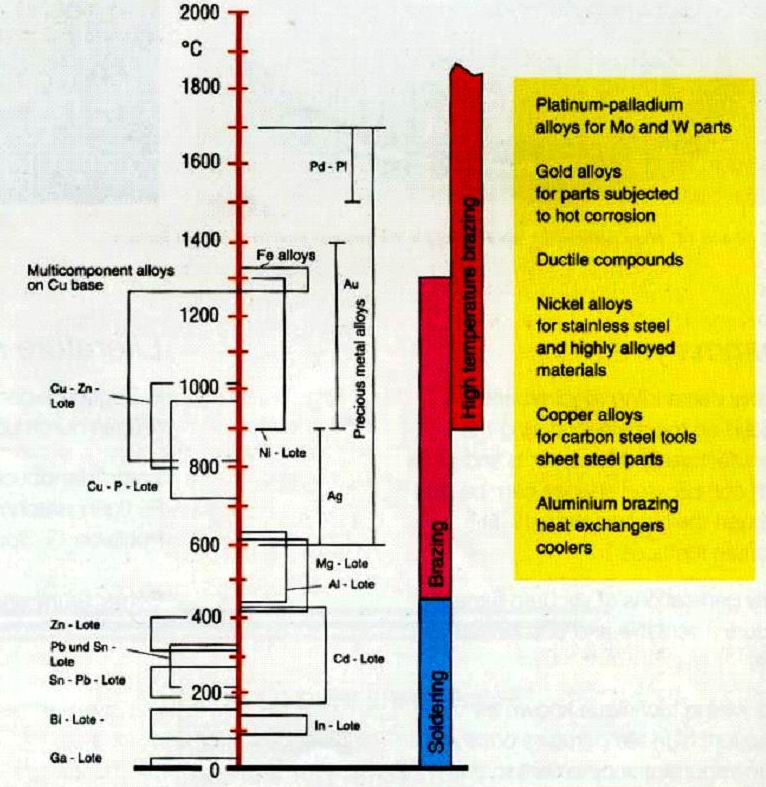
|